Nothing says specialty substrates like a piece of bread with a thick layer of Nutella printed on it.
My friend Guido Lengwiler, a professor of screen printing in Switzerland and the author of A History of Screenprinting, to be published later this year, sent me pictures of a little test he has his students run.
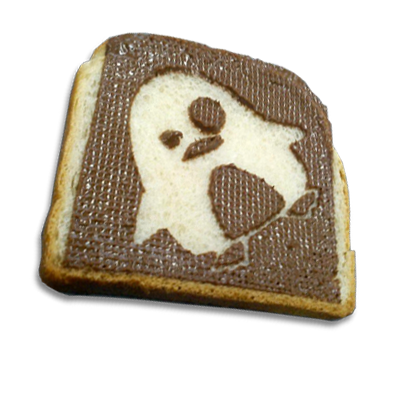
The point of the experiment is to show the versatility of the screen-printing process, how it can print almost anything in a semi-liquid state onto any type of surface. This has far-reaching significance, not necessarily as a way to provide snacks for hungry students—although I hear it tastes really good after a pass through a tunnel dryer—but in the world of manufacturing, where the ability to print one material onto another has revolutionized how things are made.
The very concept of printing has evolved all around the world. For 500 years, imprinting paper was about as exotic as it got, and the primary purpose of printing was putting words, and then illustrations, on paper. Wallpaper and fabric printing stretched the uses of the printing processes, but it wasn’t until the late 1800s and early 1900s that printers ventured into specialty materials, ceramics and metal being the main recipients of ink. The main purpose was decorative, again with words and images. Ink on paper is still big, five centuries after Gutenberg, with digital and offset or combinations of the two processes dominating. And that’s how the general public, a lot of the print trades, and the education system for the most part still see print.
What is printing?
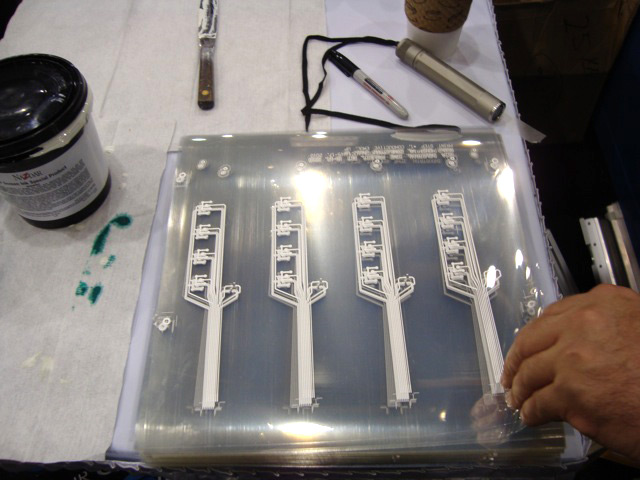
Let’s face it—once we walk out of the screen shop, factory, or material-science lab, if you ask 1000 people to look up from their smartphones for a second and touch or point to the print nearest to them, none will hold up the phone. Yet, the backside of the touchscreen has conductive and luminescent material printed all over it. That’s how it works: One non-traditional ink is printed on a non-traditional material. Modern manufacturing using a printing process—who’d have thunk it? Put the two together and pretty soon you have a new product—in this case, $63 billion worth of iPhones and iPads or their clones this year in the USA alone.
In the past, offset, flexo, and gravure offered the ability to print a narrow range of inks on some substrates other than paper. The main restriction, if the ink could be formulated to adhere, was that the material had to be thin and come in rolls. When screen printing stuck its pointed, little head through the first bolt of silk, it started a print revolution that continues to this day.
"No longer just a pretty picture, the printed images and their substrates were now circuits that would conduct electricity and perform a job.”
Glass, metal, wood, and cloth were the original specialty substrates, and screen printing was uniquely capable of decorating them. They required specific inks able to durably bond to the material and, of course, to be printable. The flexibility of screen printing allowed for this. You had a screen, mesh, and stencil combination that you could adjust easily to accept any ink, along with a press setup that could adapt to any size, shape, or thickness. Along comes plastic in all its types, and a whole new set of problems—and ink solutions. The advent of printed electronics demanded not only durability, adhesion, and printability, but it also threw in a fourth curve: functionality. No longer just a pretty picture, the printed images and their substrates were now circuits that would conduct electricity and perform a job.
Screen printing has been a leader through all of this, although inkjet inks have evolved since the mid 1990s to print an ever-broadening range of material. The problem of imaging rigid, dimensional material was solved with flatbed digital printers, and there is no question that when it comes to short-run, full-color graphics printing, digital is here to stay—even when the material is a sheet of plastic or metal.
What’s ahead?
Functional printing is driving our sector into, or should I say onto, even more exotic materials. The combination of specially formulated inks and substrates has given us an amazing array of new products and new ways to manufacture old ones. As a screen printer, I’m proud of the old squeegee and what it continues to produce: a dermal patch, a solar panel, a fuel cell, a flat battery.
Where do we go next? That's hard to say. There were no iPhones ten years ago. Far fewer people used the Internet 15 years ago, when ecommerce was only an idea. Wide-format digital was just a rumor 20 years ago. But as long as there are creative people with ideas who are willing to test out a concept, then expect to see more printing on an expanding range of materials. If it is done by screen printing, or digital, or one of the other print processes, I’m sure the method will be decided by what works best.
Over the years, I’ve printed on a lot of challenging materials: 3D parts, metal, plastics, carbon fiber, even drums made of deer hide. But the weirdest one by far was edible dog chews. A retired dentist had this concept—gift cards for dogs. But instead of cardstock, he wanted it to be something a good dog could truly enjoy. He tracked down some edible ink and some sheets of rawhide—Not the greatest material, but with some experiments with mesh and squeegee hardness, we got it to work. I never did taste them. The Nutella on bread? I may have to give that a try.
Originally printed in the February 2013 issue of Screen Printing Magazine.
